Manufacturer cover buttons from fabric and leather. Manual
Pulling the buttons from the fabric.
The appearance of the blanks stitched buttons:
Typically, this slightly arched aluminum Cup and the plastic substrate is black or white. Also used metal substrates.
Note: Pulling the buttons for clothing with the metal substrate is not very good for clothes as quickly frays the thread, which is sewn a button. Often complained by the customers. But these details are well suited for making furniture buttons.
The button blanks are sold: for No. 16-36 of 500 pieces of the same color.
No. 44-60 packing 250 PCs one color.
Most often in Russia sell blanks for pulling buttons brand "Micron"
But sometimes there are other Turkish brands or
And as the company Protos offers blanks for pulling buttons produced by “BIG” of Greece.
Color black and white. Packaging 1000 PCs of one color.
The manufacturing process of pulling the buttons is not difficult, it is important to have the necessary tools.
There are 3 main types of nozzles for the manufacture of the tight buttons.
(The terms used by different companies such as Nozzles, Punches, Matrixes, Cartridges)
1. Tips for press TER-1
2. Tips for press D-1 (and for all presses percussion)
3. Tips for making pulling double presses of buttons for D-2 and D-3.
Tips for covering buttons to press TEР-1 (can be Used on any press)
Tips for making the tight buttons have the following diameters corresponding to the diameters of the blanks:
No. 18 diameter = 11 mm
No. 20 diameter = 12 mm
No. 22 diameter = 14 mm
No. 24 diameter = 15 mm
No. 26 diameter = 16 mm
No. 28 diameter = 18 mm
No. 30 diameter = 19 mm
No. 32 diameter = 20 mm
No. 36 diameter = 23 mm
No. 40 diameter = 25 mm
No. 44 diameter = 28 mm
No. 50 diameter = 32 mm
No. 60 diameter = 37 mm
Each nozzle consists of four parts:
Once the workpieces to pulling the button - blanks brand Micron sold in the companies Veltex, strong, Ultratex, Gamma, Odeon, Mage and other and Sundry.
The manufacturing process of pulling buttons through the nozzles for the press TEР или СЕМ. 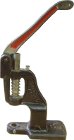
From fabrics intended for the manufacture of buttons, cut into strips
size: Ø buttons + 1 centimeter.
Then the strip is cut into squares, and cut the corners of the fabric squares.
The button blanks from a fabric finish.
Tip: to speed up the tedious process of cutting pieces of fabric, fold the cut strips of fabric in 2 or 3 or 4 layers (depending on tissue thickness) and cut into squares, and then 2-4 layers of fabric) cut the corners of the squares. A big time saver.
The work piece of fabric to cover the buttons do so with the help of a special cutting tool.
The sequence of pulling the manufacture of buttons:
The scheme of manufacturing:
Due to the required nozzle is easy to make any number of pulling buttons.
For example: 100pcs. No. 18 for wedding dress
Tips:
- With the help of nozzles for the same it is possible to make pulling the buttons from leather and leatherette.But you must consider that leather (leatherette) can be damaged by sharp edge parts of the nozzle.
This edge is slightly to grind off a whetstone or a file (but without fanaticism).
Sometimes pulling on the buttons still breaks the surface layer of natural or artificial leather. Toposheet for two reasons:
1. You need to keep in mind that this nozzle creates a large surface tension of the material from which we manufacture cover the button.
2. Low quality material (most often)
The work piece of fabric to cover the buttons do so with the help of special felling
But there are disadvantages:
1. Felling large diameter are not suitable for manual presses TER, SEM, strong. But with a strong desire to make an adapter.
2. It is necessary to expend funds for the purchase of this tool. For each diameter buttons has cutting-piercing.
3. To find the storage location to deforestation were on hand and a long search for.
4. Does it make sense to use logging if ordered 5 buttons of the same diameter and 3 buttons of a different diameter. More time will be lost when changing the cutting tool.
5. When working with synthetic fabrics cutting quickly blunts, you need to pay a specialist for re-sharpening.
Conclusion: Easier and faster to cut workpieces ordinary tailor's scissors.
When working with silk fabrics ( chiffon, silk, satin, crepe, satin crepe, satin, taffeta and organza) must make a piece of two layers of fabric, or glue a thin adhesive dublerin.
You can do the following: notify the customer or to glue dublerin tissue and increase order value by 50%.
However, the buttons are made of silk fabric weaving't turn out perfectly round. If you look closely it is evident that the fabric is folded corners. But keep in mind that the background of the product of this small defect will not be noticeable:
To deal with this phenomenon is useless. To smooth the deformation you want to duplicate an adhesive cloth or make the workpiece in two layers of silk (satin) and put it inside each other.
Note that when working with such types of fabrics like taffeta, organza, crepe satin, crepe satin, stretch their varieties, both natural and synthetic fibers.
- In Asia the prevalence of fabrication pulling buttons for children's clothing.